When information is trapped in isolated systems across the production floor, getting valuable insights is increasingly difficult, and integration becomes fragile. The result? Wasted time, missed opportunities, and inefficiencies that eat away at the bottom line.
In this article, we’ll explore the real costs of data fragmentation and how Factry Historian can bring clarity and efficiency to your operations.
The real costs of fragmented data sources
Before exploring solutions to eliminate data silos, let’s zoom in on the consequences of data fragmentation for your industrial business.
1. Inefficiencies due to operational firefighting
Inefficient operations are one of the most immediate consequences of data silos. Think about all the hours managers spend pulling information from different sources, verifying if it’s correct, and trying to reconcile conflicting data. To then end up with an Excel sheet containing data they don’t even really trust. It’s a tedious process that distracts managers from the actual work they should be doing, such as analysing production data and making impactful decisions.
2. Delayed data projects and lack of innovation
As a result of fragmented data sources, and a lack of a centralised IT infrastructure, it becomes significantly more challenging to set up data projects. Without centralised data management, each new data initiative requires building a separate infrastructure, leading to high costs and increased complexity.
This approach slows down the ability to launch and scale projects effectively, and these delays accumulate, ultimately dragging data projects out longer than necessary and stifling innovation.A central platform reduces the marginal costs of each new data project, making it easier and more efficient to drive continuous process innovation.
3. Cumbersome decision-making processes
Another significant problem that data silos create is delayed decision-making due to a lack of oversight on production operations. Fragmented data forces managers to scramble across the production floor just to understand how production is running. This results in production errors or quality issues being noticed too late, and missed opportunities that could have been avoided with the right information at the right time.
Ultimately, these inefficiencies add up, leading to increased operational costs and reduced overall profitability. By centralising data sources, managers can follow up on production from wherever they are, and make timely, informed decisions to improve efficiency and reduce costs.
4. Lack of collaboration between departments
Data silos not only hinder efficient operations but also create barriers between departments, limiting the ability to work together effectively. By eliminating data silos, and automating data processing, every department — from operations to facility management, maintenance and engineering — can access the same reliable production data without delays.
This unified access fosters collaboration between people and departments, driving continuous improvement and cost reductions in both the short and the long run.
5. Risk of decreased customer satisfaction
The consequences of data fragmentation aren’t just about cold hard cash alone. Customer satisfaction can take a serious hit without a clear view on your production processes. If production data is scattered across multiple systems, it takes a lot longer to resolve issues, and product quality inevitably suffers. Clients notice these inefficiencies, and it can lead to frustration and loss of trust.
Additionally, scattered process data makes compliance a nightmare. Disconnected systems make it hard to track and prove compliance with regulations, increasing the risk of reputational damage. In case of a client complaint, this will probably mean searching for manually written data on paper, taking hours when you need the information immediately.
As illustrated, data fragmentation is nothing less than a drain on operational efficiency, decision-making, and competitiveness.
It creates obstacles across every department, from missed innovation opportunities to dissatisfied customers. However, disjointed process data isn’t something you’re stuck with forever.
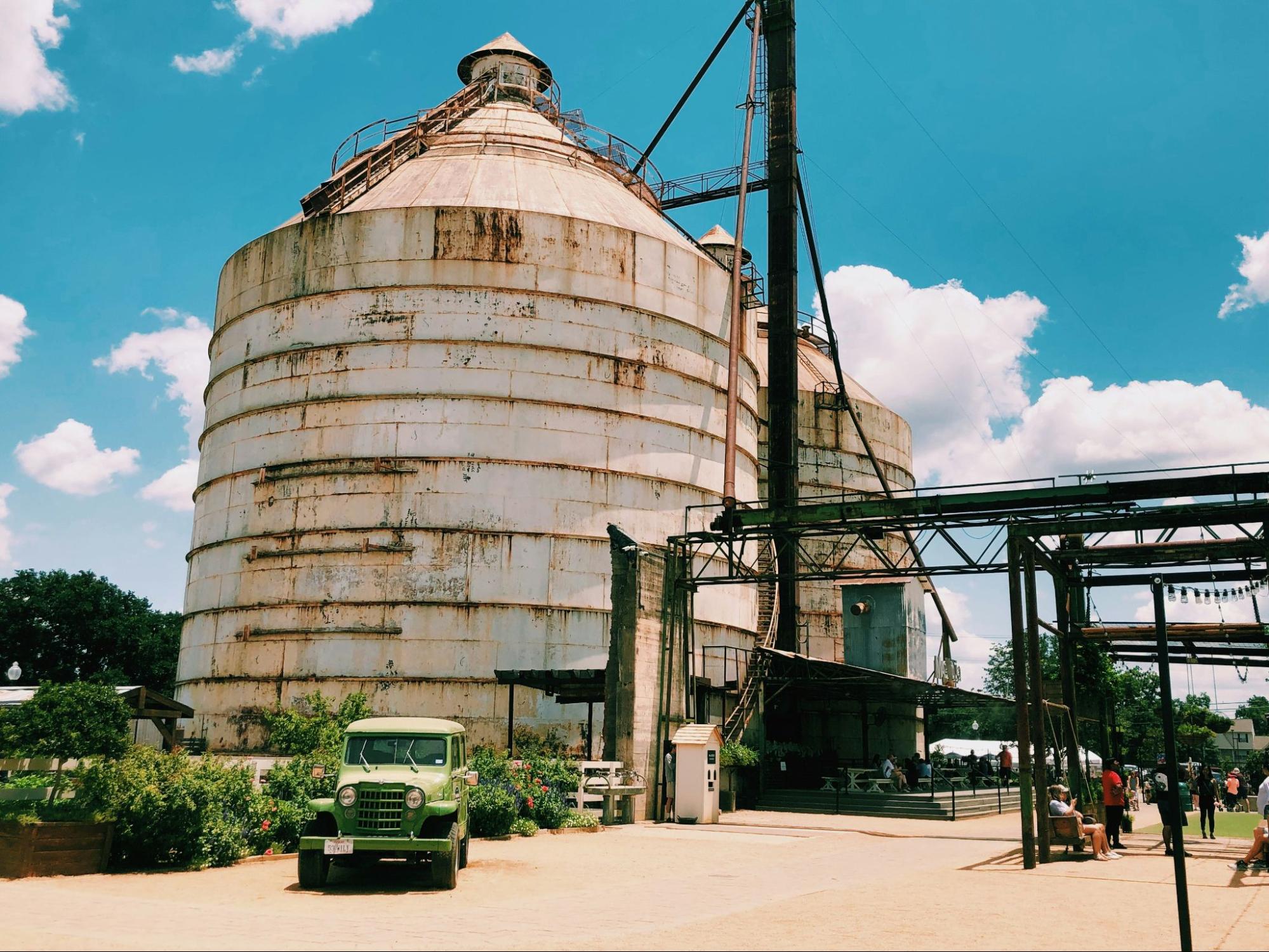
The value of a centralised platform
A centralised data platform ties everything together, providing real-time insights into production operations, eliminating manual data processing and facilitating collaboration across all departments. As such, it lays the foundation for continuous improvement.
1. Better collaboration across departments
A centralised platform means central trust in the data. Once data is validated, the conversation shifts from debating the right data source to drawing the right conclusions for operational improvement. With data available at the IT level for everyone, cross-functional collaboration becomes much easier, which is essential for driving meaningful change.
2. Cost-effective data project implementation
The hard work lies in connecting data sources and collecting relevant information. With a centralised platform, the data is already in place, eliminating the need to set up new projects with multiple stakeholders (IT, OT, automation) just to get started. This speeds up implementation and saves costs.
3. Real-time insights for better decision-making
With always up-to-date data, decision-makers can anticipate and resolve issues proactively, avoiding costly production delays, inefficiencies and errors. This visibility also improves the accuracy of planning and forecasting, enabling better resource allocation and reducing waste.
4. Improved operational efficiency
A centralised platform eliminates manual processes, radically reduces time spent on reconciling data, and allows teams to focus on high-value tasks. This efficiency boost not only optimises day-to-day operations but also ensures that resources are used where they create the most value.
And the best thing of all? The benefits of a centralised platform compound over time, without the escalating complexity and costs associated with fragmented systems.
Factry Historian as a central data platform
Meet Factry Historian.
Factry Historian is designed to collect, process, analyse, and integrate process data, helping your organisation move beyond data silos. It provides a unified view of all your data, transforming scattered information into a single source of truth within a unified interface. This makes analysis easy, eliminates manual work, and provides teams with the insights they need when they need them.
With Factry Historian, you get a solution that brings it all together — centralising data that is easily accessible, providing real-time insights, and fostering collaboration between people and departments. The result? A streamlined, cost-effective approach to data management that empowers your organisation to thrive today and in the future.
- Save costs - No more manual work, fewer tools to manage, and a simplified IT landscape mean lower costs and increased productivity. Everything flows seamlessly, cutting down wasted time and resources.
- Increase operational efficiency - By eliminating manual processes and data inconsistencies. You and your teams can finally focus on high-value tasks instead of wrestling with disconnected information.
- Get real-time process insights - With always up-to-date information and clear dashboards, managers and machine operators can make proactive decisions rather than reacting to issues after they arise.
- Make better decisions - With Factry Historian, data-driven operations become a reality. Make calls based on facts, not intuition or assumptions. This confidence in data leads to smarter strategies and better outcomes.
- Set up data projects cost-effectively - A central platform, like Factry Historian, reduces the marginal costs of each new data project, making it easier and more efficient to drive continuous process innovation.
- Make compliance manageable - A consolidated data platform makes regulatory and client reporting straightforward, with all relevant production data available in an organised format within seconds.
Factry Historian isn’t just about adding a layer of convenience. It’s about laying the groundwork for data-driven operations, transforming how you work.
On top of that, and in contrast with traditional data collection solutions, Factry Historian offers your business unlimited scalability and flexibility. Whether adding new data sources or expanding operations to additional sites, the system scales seamlessly and cost-effectively, avoiding the traditional challenges associated with legacy systems or patched-together solutions.
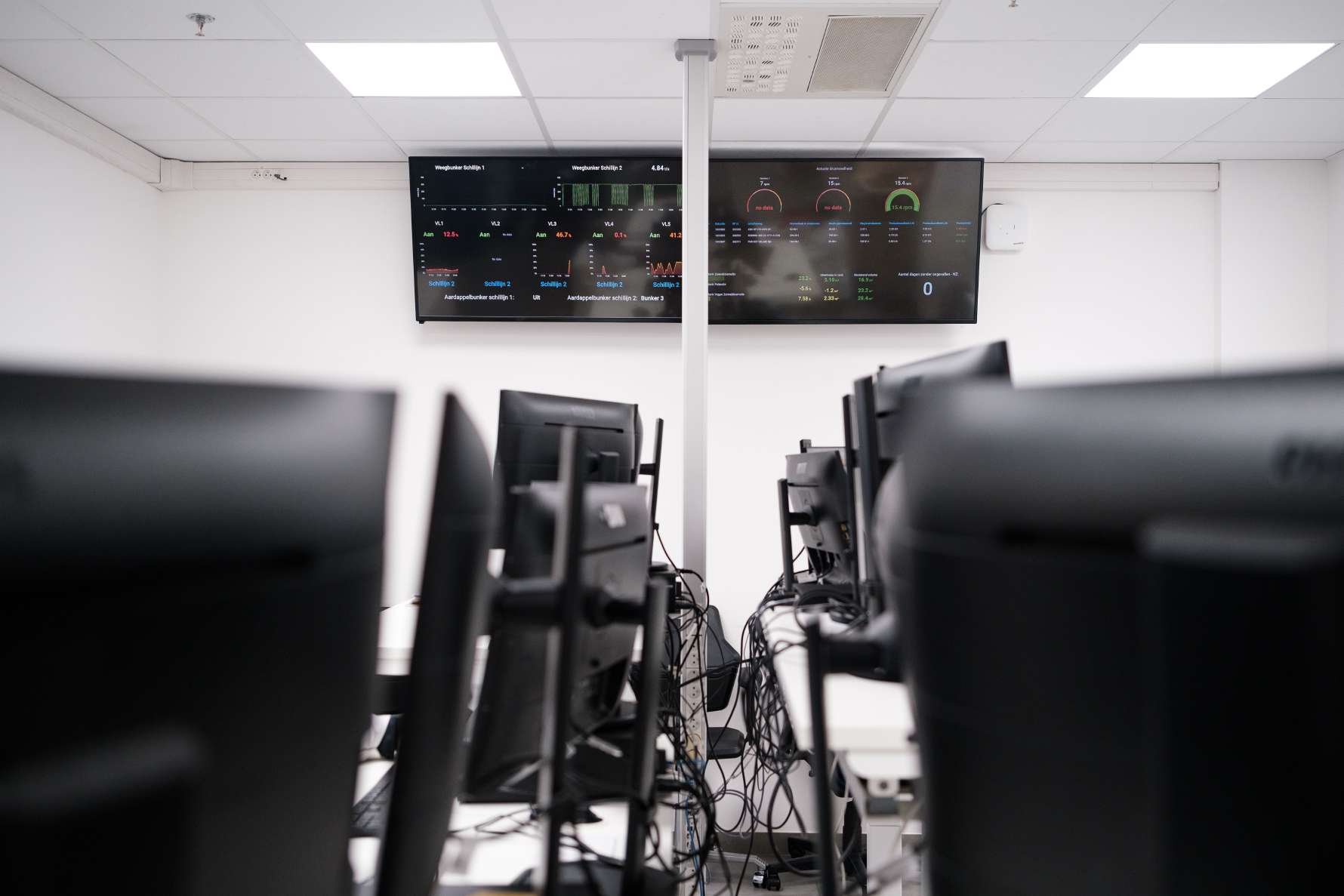
Eliminating data silos: Factry Historian in use
Here are some real-world examples of how Factry Historian is making a difference in eliminating data silos, and improving the bottom line:
AGC Glass Europe
AGC Glass Europe faced significant challenges with data scattered across multiple production sites. Disparate systems led to inconsistencies and inefficiencies, often causing downtime and bottlenecks.
By implementing Factry Historian, AGC Glass digitised data collection across multiple sites, consolidating everything into one unified platform, ready for operational analysis. This eradicated manual data entry, improved transparency, and enabled better decision-making by centralising their previously fragmented data.
At the same time, by integrating Factry Historian with business analytics tools, it enables advanced insights the management can act on.
Roger & Roger
Roger & Roger, a leading Belgian producer of potato snacks, faced challenges with fragmented data across their production sites. This fragmentation led to inefficiencies and hindered their goal of operational excellence.
By implementing Factry Historian, and FactryOS, they unified their data management across sites, enabling real-time insights into production processes. This centralisation facilitated the identification of trends and improvement opportunities, reduced reliance on manual data entry, and supported informed decision-making.
The results: enhanced operational efficiency, streamlined data management, and a company-wide culture of continuous improvement.
Tear down data silos, improve the bottom line
Discover how Factry Historian eliminates production data silos, tackles inefficiencies, and helps your organisation make better, faster decisions.