How can food manufacturers continue to compete with the biggest corporations in an AI-driven world? Find out how advanced process data analysis, along with integration with other tools and technologies, can improve the bottom line and secure competitiveness of companies in the food and ingredients industry.
Top challenges for food industry companies
Food, beverage, and ingredients producers face the same basic challenges as other manufacturers: streamlining quality, increasing productivity, and gaining visibility into the production process to make data-driven decisions.
However, due to the specific nature of the food industry—where factors like ingredient variability, small batches, and rigorous regulatory standards come into play, the complexity and scale of these challenges is heavily amplified.
Increasing data volume and velocity
One of the key challenges for food companies in implementing effective traceability and transparency systems is managing the extreme amounts of data generated by machines and processes. From sensor data on process KPIs to quality control records, the data flow is continuous and will only keep growing.
Smaller batches, increased complexity
The trend towards smaller, more customised product batches in the food industry increases complexity and data management challenges. Each batch requires specific parameters, tracking, and documentation, adding to the data burden, and intensifying the pressure on existing systems and resources.
Emphasis on compliance and traceability
The food industry is extremely regulated, with stringent requirements for traceability, food safety, and quality. Recalls should be avoided at all costs, and in case of an audit, food companies must be able to deliver exact process data almost immediately. However, data is often in spreadsheets or on paper.
Rising demand for sustainable products
Clients and end consumers are increasingly demanding sustainable food products. This demand requires companies to track and report on a variety of sustainability metrics. Managing and integrating this data presents a significant challenge, especially for smaller food manufacturers.
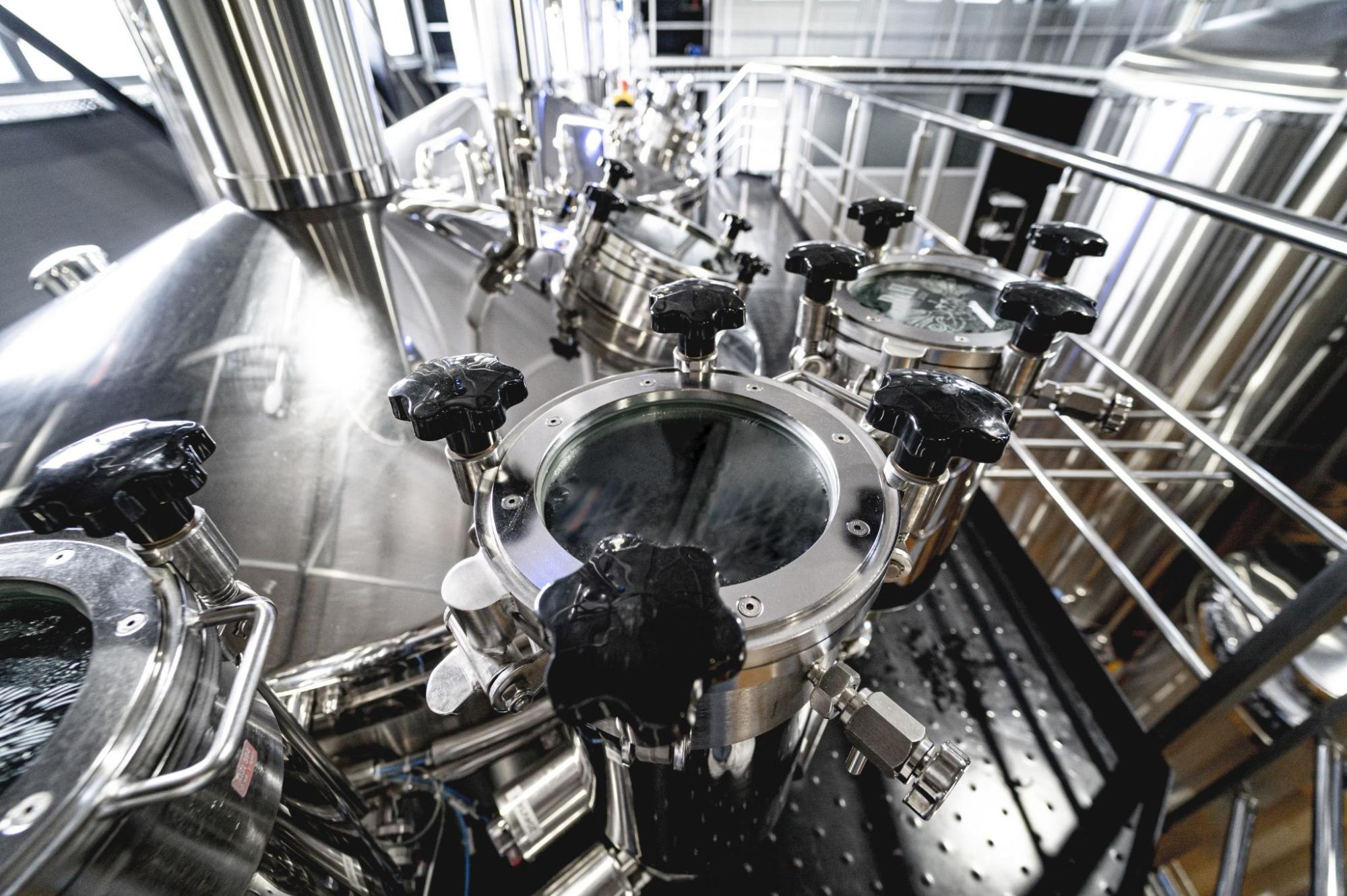
How food companies can stand their ground
The world’s biggest food corps are heavily investing in digital technology and AI.
To keep up and achieve true digital transformation without overwhelming costs, companies in the food industry need to strategically leverage modern, flexible technologies.
Here’s why, and three key ways to do so:
1. Leverage the power of open technologies to increase data visibility across the organisation
Let’s start with the basics.
Establishing a foundation for digital transformation starts with collecting data in real time from various systems, machines, and equipment. However, simply gathering data is not enough. The real challenge lies in processing and contextualising to turn that raw data into decision-making information, and making this data accessible across the organisation.
A crucial component of any manufacturer’s digitisation journey is the adoption of a modern data management solution, particularly a data historian.
Traditional proprietary historians are often costly and difficult to scale. In contrast, a historian built upon open technologies offers a more flexible, scalable and cost-effective solution.
By using open-source technologies for data storage and visualisation, you can avoid the limitations of pay-per-use pricing models, and make critical data accessible to everyone in the organisation, from machine operators monitoring real-time KPIs to process engineers troubleshooting production issues.
What’s more, the Event Module in Factry Historian automatically aggregates raw process data in the context of specific events, such as orders, products, batches, or downtime.
This allows you to quickly answer very specific questions, such as:
- How much materials or energy did an order consume?
- Which production lines or sites are underperforming?
- How does the pH-curve compare to previous batches?
- What volume was produced on a certain asset in 1 week?
- What is the energy use of an asset compared to others?
Overall, this frictionless data accessibility not only enhances operational efficiency but also fosters a culture of data-driven decision-making throughout the organisation, which is the essence of true digital transformation.
2. Facilitate advanced business analytics through real-time integration with BI tools
Now that your data is consolidated and accessible, it’s time to get the most out of it by integrating it with your Business Intelligence (BI) tools such as PowerBI or Tableau, along with a variety of other data sources.
This enables you to answer business questions such as:
- Why has unplanned downtime risen this quarter?
- Why is a certain line less productive than an identical line on another site?
- Why has our OEE decreased?
- Why is my waste cost running significantly higher this month?
Also, this step opens up an array of opportunities for even deeper analysis:
- Analyse data from production processes in analytics platforms, such as Seeq, to identify trends, bottlenecks and inefficiencies, helping to reduce production costs.
- Use AI algorithms to monitor and optimise energy consumption, identifying opportunities for savings and minimising environmental impact.
- Employ predictive analytics to anticipate equipment failures, reducing unplanned downtime and optimising maintenance schedules.
However, it is easier said than done when leveraging data from traditional historians, notoriously famous for their lack of connectivity features.
In contrast, Factry Historian provides seamless connectivity with any BI tool and analytics platform, allowing data scientists to combine real-time and historical process data with other critical information, such as MES data and supply chain metrics.
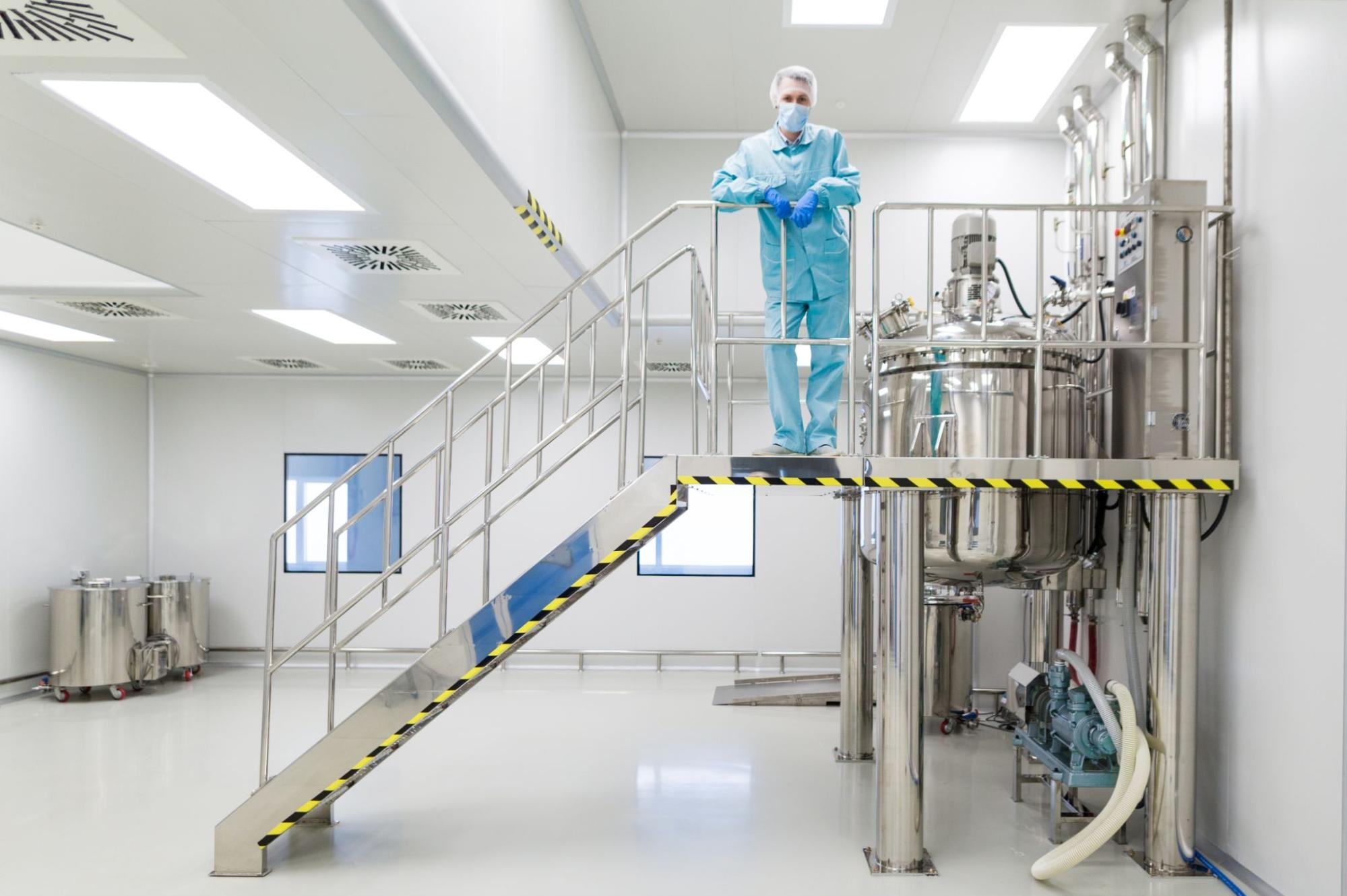
3. Feed your structured process data to AI tools to grasp the same insights as the big players
To remain competitive, food manufacturers must prepare for an increasingly data-driven future. The effectiveness of AI in enhancing production and operational efficiency depends on the foundation of structured, accessible data.
Without a robust data infrastructure, AI tools cannot deliver the insights needed to optimise processes, predict trends, or automate decision-making.
As we pointed out in a previous article, future success will not be defined by production capabilities alone but by how effectively companies manage digital transformation. A solid data foundation is crucial, as it allows your company to integrate AI seamlessly, driving huge potential improvements in areas like predictive maintenance, energy efficiency, and process optimisation.
Open technologies play a vital role here, offering the flexibility needed to adapt to future applications, whether AI or beyond.
By focusing on building this strong data infrastructure today, food companies can level the playing field with even their largest competitors, ensuring they remain agile and innovative in an unpredictable market.
Factry Historian: a perfect fit for the food industry
Factry Historian offers a robust platform for capturing, storing, and analysing the huge amounts of data generated throughout the food production process. It allows you to uncover new insights from your data to enhance quality and productivity and eradicate unplanned downtime, while providing any employee with real-time visibility into every aspect of the production process.
By consolidating data from various sources, including sensors, equipment, and other systems, Factry Historian provides a unified, detailed view of your operations. Through the Event Module, monitoring and analysing batches or other events becomes easy. It plugs neatly into any other tools such as BI or AI applications, facilitating advanced business analysis and process innovation.
Real-life use cases: streamlined data management in the food & ingredients industry
Discover how data collection, analysis and integration with Factry Historian has enabled digital transformation in the food and ingredients industry.
Puratos group (bakery industry)
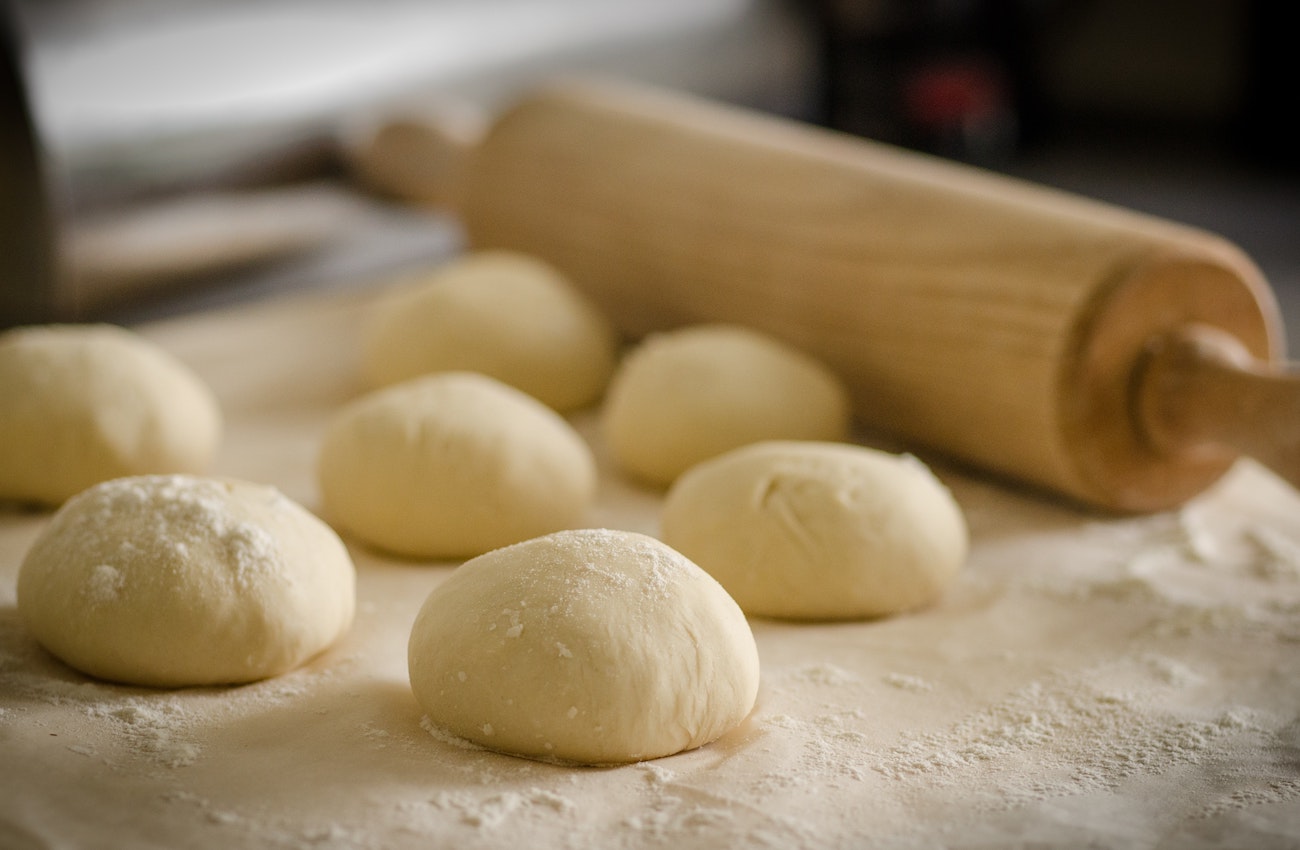
Puratos group is a multinational organisation developing ingredients and solutions for the bakery industry, present in over 70 countries.
Before implementing Factry Historian, Puratos’ process data was only available for a restricted period of time, for a limited number of users, and solely on-site.
We set out to better collect, store and visualise the company’s manufacturing process, making production data instantly accessible to those who need them.
Through radically reduced complexity and real-time process insights, the company now notices less unplanned downtime, lower maintenance costs, and higher employee satisfaction.
Agristo (potato processing)
Established in Belgium, Agristo specialises in the production and distribution of frozen potato products, and is present in 145 countries.
To streamline and refine its production operations, they implemented Factry Historian across four sites, enabling a unified data structure, fluent access to data insights, and real-time connectivity with their BI tool.
Ever since, Agristo has fostered a culture of continuous improvement, leading to significant gains in efficiency, reduced downtime, and an increase in production output.
Fire up digital transformation with a flexible data historian
Struggling to get the most value out of your process data? Schedule a demo of Factry Historian to discover how it can help you improve the bottom line.